ThaiBev is committed to reducing landfill waste from its manufacturing processes by tracking and managing waste generated within its operations through a team responsible for ISO 14001 certification. This team records waste generated from business operations to maximize efficiency and identify new projects or integrations in waste conversion. The following projects are part of our pursuit of zero waste to landfill certification and achieving our goal of zero landfill waste by 2040.
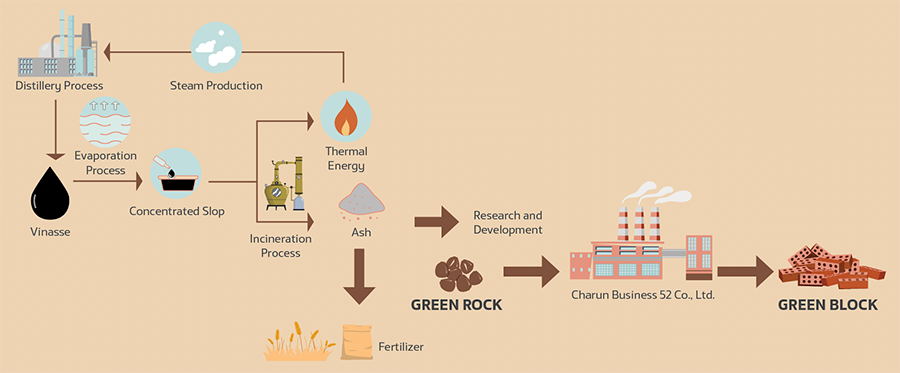
A subsidiary of ThaiBev, Feed Addition Co., Ltd., (FAD) is tasked to research and explore innovations to create values from waste. FAD collaborates with external parties, such as universities, to convert waste into higher-value products. ThaiBev has invested 3,150,000 baht in continuous research and development.
In collaboration with the National Science and Technology Development Agency (NSTDA), ThaiBev has developed
a lightweight aggregate, known as Green Rock, using the powdered ash from the incineration of concentrated slop
in the distillation processes. This material is mixed with concrete to create another value-added product called Green Block that can be used for both internal and external wall construction of buildings in tropical climate zones.
Green Block is an innovative environmentally friendly construction material that is made from approximately 10–15% recycled raw materials, through a production process that does not involve burning or steaming. Green Block’s unique feature is double ventilation technology, as the porousness of the Green Rock increases the efficiency of
air flow, helping to effectively remove heat from the wall,
and the water absorption rate is less than 14%, helping to prevent wall cracking. Green Block is certified according to Made in Thailand and Material ConneXion standards.
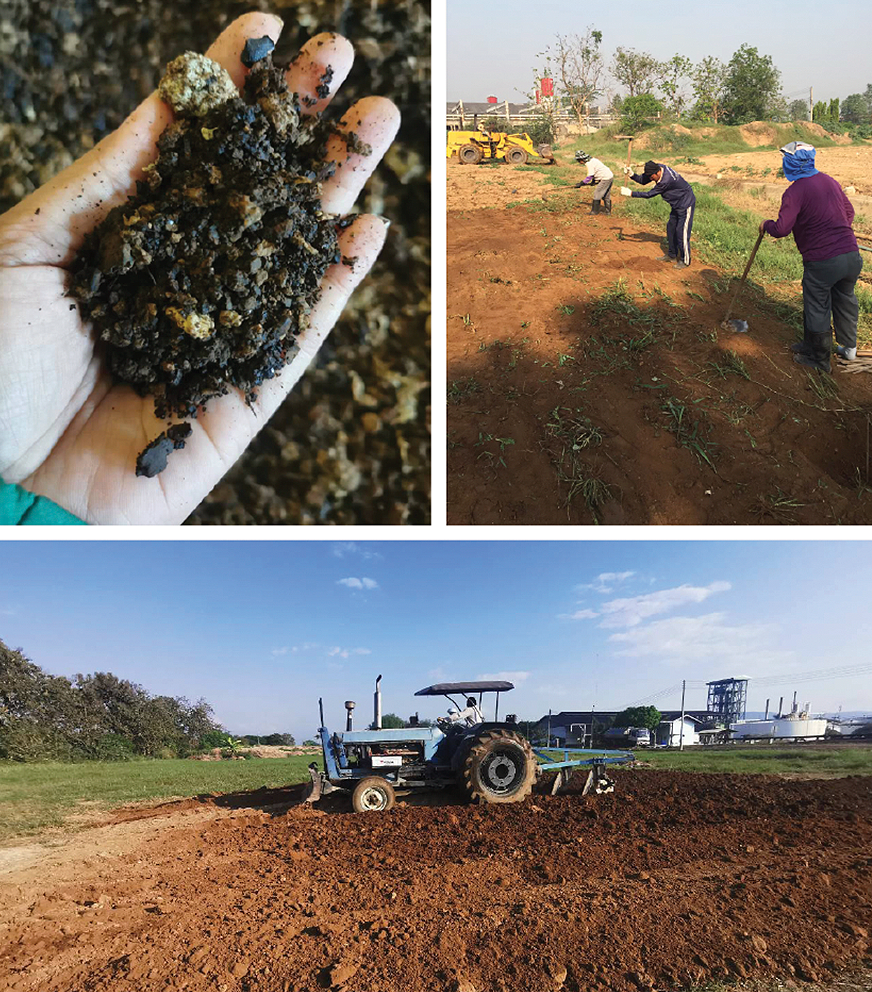
ThaiBev reuses close to one billion glass bottles in our production process annually, and one of the major types
of waste generated from the bottle-rinsing process is
label scraps. Apart from using them as fuel, several other initiatives have been put in place to prevent these scraps from ending up in the landfill.
Thanaphakdi Distillery, Chiang Mai Province, is conducting
an experiment on using label scraps as an ingredient in soil improver, which would reduce the amount of waste disposed by 8.5 metric tonnes. A trial plot of long-term crops is being grown with soil improvers containing label scraps and concentrated slop from the distilling process. The soil from the trial plot has been collected for nutrient analysis at ThaiBev Spirits Technical Services to test for soil compounds and their possible impacts on crop yield.
Lakchai Distillery, Ratchaburi Province, sends label scraps to Eco Friendly Thai, a company that upcycles pulp from used packaging. In 2023, Lakchai Distillery has sent 11.67 metric tonnes of label scraps to be recycled into plant pots and other home decor items.
ThaiBev have a team responsible for ISO 14001 certification. across all business divisions and launched a comprehensive waste audit initiative as part of its commitment to achieving zero waste to landfill by 2040. This program aims to assess the waste data of each production process , analyze waste data in order to reduce the amount of waste going to landfill, and identify opportunity for improving waste performance.
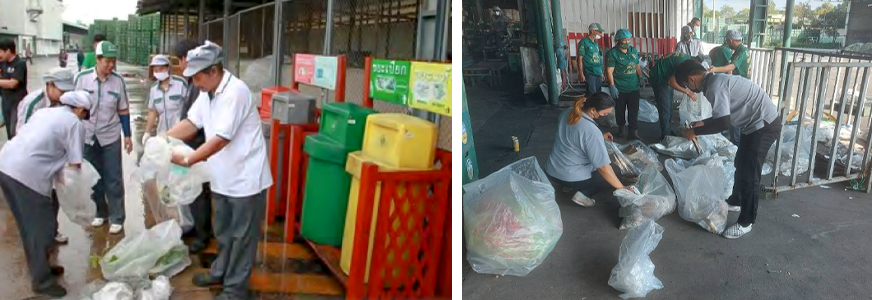
Encouraging Employees to Participate in Waste Reduction by Separating Waste
To reduce the amount of waste sent to landfills and promote the most efficient use of resources through the 3Rs principle, ThaiBev’s production facilities have launched a campaign to create awareness among employees about the benefits of waste separation and the value that can be added to recyclable waste. The results of the campaign are as follows:
- Reduction of waste within the factories and to landfill
- Ability to recycle waste for other uses
- Creating teamwork among employees
- Reducing costs and adding value to waste
- Reducing waste-related impacts and protecting the environment
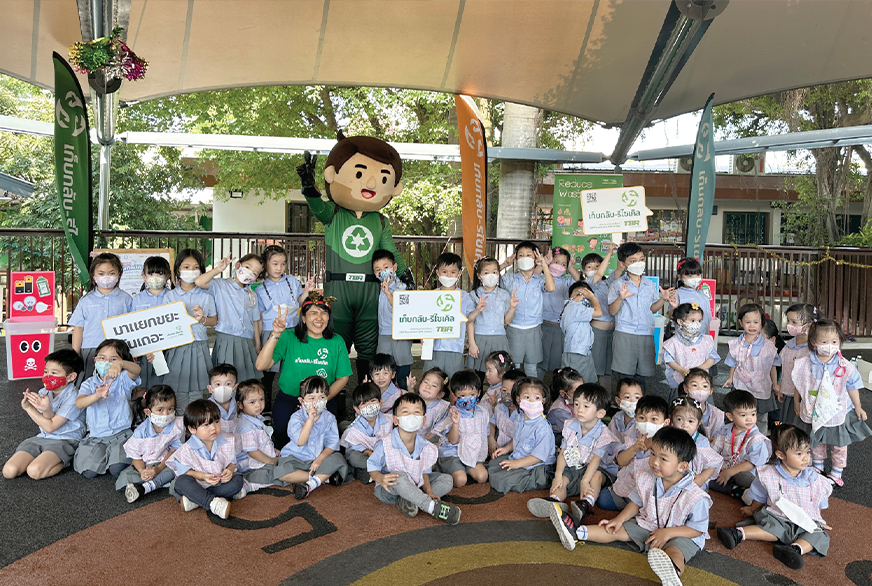
ThaiBev has extended the Bring Back–Recycle campaign
to the younger generation in order to provide education on the importance and benefits of waste segregation. In 2023, ThaiBev engaged with 300 pupils from 40 schools in the CONNEXT ED, Partnership School, and Our Khung Bang Kachao projects to teach them how to properly separate each type of waste at source. Throughout the program, ThaiBev provides continuous support for these schools from baseline measurement to measuringthe impacts from their participation in the campaign. Apart from the reduction
of waste being disposed to landfill, participating schools have carried out more advanced activities such as establishing waste management clubs and/or working groups,
and turning waste into more valuable products that can generate additional income.
2023 Performance (Unit: Metric tonnes)
Waste by type and disposal method (Unit: Metric tonnes)
Total weight of waste generated |
43,503 |
38,774 |
54,725 |
84,260 |
Total weight of waste diverted from disposal |
36,623 |
33,169 |
44,134 |
72,375 |
Waste that is reused / recycle /sold |
36,623 |
33,169 |
44,134 |
72,375 |
Total weight of waste directed to disposal
|
6,880 |
5,605 |
10,591 |
11,885 |
Waste disposed to landfill |
5,945 |
4,640 |
4,350 |
4,135 |
Waste incinerated with energy recovery |
547 |
599 |
5,863 |
7,325 |
Waste incinerated without energy recovery
|
354 |
356 |
368 |
423 |
Wasted otherwise disposed |
34 |
10 |
10 |
2 |
Total weight of onsite composting and landfilling |
N/A |
N/A |
N/A |
14,030 |